Implementing Advanced Ladle Health Monitoring at a Large Integrated Steel Plant
Client: A Large-Scale Integrated Steel Plant
Industry: Steel Manufacturing
Challenge: Improving ladle tracking, health monitoring, and lifespan management in a high-demand Steel Melting Shop (SMS), while significantly improving ladle turnaround time, directly contributing to increased ROI.
Solution: Implementation of a comprehensive Ladle Management System (LMS) using cameras for location tracking and imaging cameras for health monitoring.
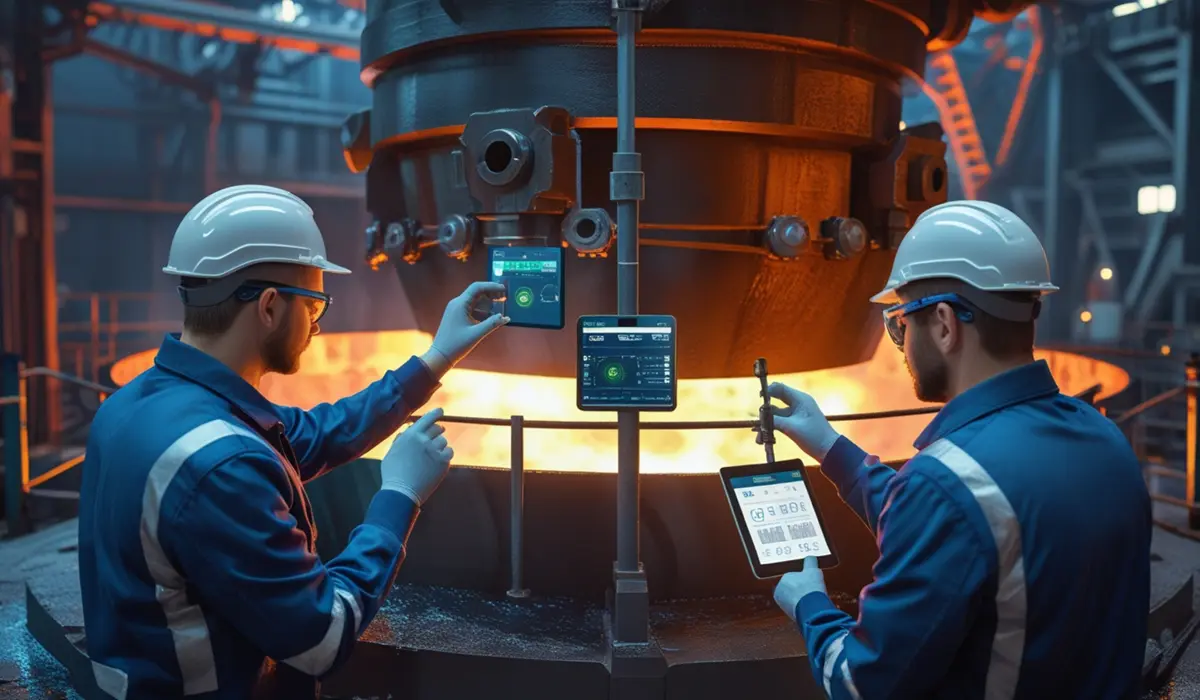
Introduction:
The Need for Smarter Ladle Management
A major integrated steel plant, operating a high-throughput Steel Melting Shop (SMS), recognized the need to upgrade its ladle management practices. Ladles are critical, high-wear assets in steel melting, and managing them effectively impacts safety, production schedules, and costs. The plant aimed to move beyond traditional methods towards a modern system that could track ladles accurately, monitor their health in real-time, and optimize their usage to extend their life. They partnered with Epsum Labs to develop and implement this advanced solution.
The Challenges:
Limitations of the Existing System
Before the project, the plant faced several operational difficulties related to ladle management:
Manual Tracking Inefficiencies
Keeping track of dozens of ladles – their location, status, and usage cycles – relied heavily on manual logs and visual checks. This process was time-consuming and sometimes led to errors, causing delays in finding available ladles when needed for production, ultimately decreasing operational efficiency and compromising the ROI.
Preventive Maintenance Risks
Ladle health, particularly the condition of the refractory lining, was mainly assessed during scheduled maintenance or, unfortunately, after a problem or failure occurred. There wasn't a reliable way to monitor wear and tear or detect early warning signs of potential issues like cracks or excessive thinning. This reactive approach carried significant risks, including potential molten metal breakouts (a major safety hazard) and unexpected production stoppages.
Uncertainty in Lifespan Optimization
Without precise, real-time data on how each ladle was used (e.g., number of heat cycles, time spent at high temperature, turnaround time between uses), it was hard to accurately predict the remaining useful life or make informed decisions to maximize it safely. This often meant ladles were either retired too early (increasing costs) or pushed too long (increasing risk).
The Solution:
An Integrated, Data-Driven Approach
Epsum Labs delivered a comprehensive Ladle Management System (LMS) designed to address these challenges directly. The system integrated several technologies:
Automated Real-Time Tracking
Cameras were installed along the ladle movement track within the SMS, enabling automated, real-time monitoring of each ladle's exact location and status on the shop floor. Using object detection and OCR technology, the system accurately detects and identifies each ladle, with all data accessible through a centralized dashboard.
Ladle Health Monitoring:
The system collects data from thermal imaging cameras. This data was used to identify patterns and predict potential failures, such as lining wear-through or shell integrity issues, enabling timely, proactive maintenance.
Performance Optimization Tools:
The LMS automatically calculated key performance indicators (KPIs) for each ladle, such as its total heat cycles (tracking its life) and turnaround time. This data helped operators optimize ladle rotation, schedule maintenance more effectively, and implement strategies to safely extend ladle lifespan.
Centralized Maintenance Planner:
A dedicated maintenance planner module was introduced to streamline scheduling, documentation, and accountability. It helped track all agencies and teams involved in ladle upkeep, from lining contractors to inspection crews, ensuring coordinated efforts, timely servicing, and complete maintenance history for every ladle.
The Results:
Measurable Improvements Across the Board
The implementation brought significant and tangible benefits to the steel plant's SMS operations:
Enhanced Safety
Proactive monitoring and predictive alerts drastically reduced the risk of ladle failures. The plant saw a significant reduction in ladle-related safety incidents or near-misses.
Reduced Production Downtime
Automated tracking eliminated time wasted searching for ladles, and predictive maintenance prevented unexpected stoppages.
Extended Ladle Lifespan
By understanding wear patterns and optimizing usage based on real data, the plant could manage its ladle fleet more effectively, leading to an average increase in ladle life.
Improved Operational Efficiency
Streamlined tracking, automated data collection, and better maintenance planning improved the overall workflow and productivity within the Steel Melting Shop. Turnaround times were reduced significantly, contributing to smoother operations and increased efficiency.
A Foundation for Safer, More Productive Steel Melting
By replacing manual processes and reactive maintenance with an integrated, data-driven Ladle Management System, Epsum Labs helped the client achieve significant improvements in safety, efficiency, and asset utilization and an increase in ROI.
The ability to track ladles accurately, monitor their health continuously, and predict potential problems proactively has provided a strong foundation for more reliable and cost-effective steel production.
This project demonstrates the power of applying AI/ML technology to solve traditional industrial challenges.